Many factors, including weather, can cause concrete damage. You’ll need a repair material that can resist moisture and extreme temperature changes and one that can expand slightly with heat or contract with cold.
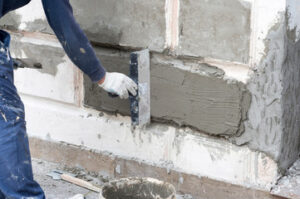
Since the full scope of work is often unknown until the damaged areas are chipped away, most engineers approve payment for unit cost items rather than a stipulated sum. For professional help, you may contact Concrete Repair Eau Claire.
Crack Sealer is used to fill in and seal small cracks in concrete. It helps protect the concrete from water, ice, dirt and other contaminants that cause deterioration. It is especially useful on surfaces that are exposed to traffic.
It is a cost-effective way to extend the life of exterior concrete. It is particularly helpful on roads and parking lots. It can be used in conjunction with chip seals, HMA overlays, slurry seals and micro seals. Crack sealing is most effective in moderate temperatures.
Prior to application of crack sealant, the area should be cleaned. This can be done by scrubbing the area with a wire brush or power scrubber to remove loose debris. It is also necessary to clean out the crack using a power washer. The crack should be routed out to a minimum of 1/4 inch wide. This allows the sealant to adhere properly to the main body of the concrete. It is recommended that a chisel be used to create a backward angled cut in the crack, as this will help keep the crack from backing out later.
Applying the crack sealant is simple. The crack sealant is heated in a machine to 380 degrees F and placed into the crack. A squeegee is then used to smooth the crack sealant to a level surface. The sealant will begin to set in 20 to 40 minutes. This is sufficient time to allow the crack to be opened to traffic.
Once the sealant has cured, the crack can be painted over. The paint will help to camouflage the crack and give it a finished look. If the crack is not to be painted, a blotter can be used to remove excess sealant from the surface. This will prevent traffic tracking on the fresh treatment and prolonging its life.
It is important to use a concrete crack filler that is designed to be flexible and stretch with the movement of the concrete. Using the wrong type of repair can lead to further deterioration of the concrete. It is also critical to avoid overfilling the crack. Overfilling can cause the crack to widen and potentially detach from the concrete.
Repairing Large Cracks
If your concrete is suffering from wide, deep cracks that are not confined to one small section, it’s likely time to call in the professionals. Attempting to fill these types of cracks with traditional patch materials can lead to the cracks resurfacing and potentially worsening over time. It’s a good idea to consult with an experienced concrete contractor to find out whether full replacement is a better option, or to try resurfacing the area with a decorative overlay that can help disguise the cracks.
The first step in repairing large cracks is to clean out the entire area. Any debris or gravel that is stuck within the crack will keep the repair compound from adhering to the concrete. It is also a good idea to chisel the crack, and to orient it in an angle back towards the body of the concrete. This creates a wider base for the crack, and prevents it from back out of the repair once it sets.
Once the crack is cleaned, it’s important to make sure that it is fully dry. Any water left inside of the crack could cause the concrete repair to fail. A sand-water mix is recommended, which can be applied with a trowel to ensure that the crack is fully filled.
It is a good idea to use a plastic sheet, such as a tarp, over the area where you’re working to protect your property from the cement. Afterwards, use a shop vacuum to remove any dust and debris from the surface.
Once you’ve finished cleaning the crack, mix your chosen concrete patch material according to the manufacturer’s instructions. It’s best to work with a small trowel to apply the patch, and to only add a 1/4″ layer at a time. When you have a small amount of patch in place, use your trowel to blend the surface with the surrounding concrete, and to make sure that it is level with the top surface.
It’s worth noting that concrete repairs will frequently produce a lighter colour than the parent concrete, as until their surfaces weather, they will not support the algal or mould growth which darkens ‘aged’ concrete. The darker colour can be offset to some degree by the use of pigments during mixing, but this only delays the process for a few years.
Repairing Holes
Concrete repairs can include patching, re-colking or re-pointing to repair joints. Concrete repairs can also involve levelling or slab jacking to raise or lower areas of the surface. A more long term approach to repairing damage is to prevent future deterioration by addressing the causes of the damage.
Concrete cracks are caused by many factors, including water movement and freeze-thaw cycles. Sealants can be used to fill the cracks and reduce their occurrence but the underlying problem must be addressed to stop the cracks recurring. The best solution is to use a concrete repair material that includes both cement and aggregate. It’s important that the correct mix is chosen to match the parent concrete and that it will weather in the same way as the existing structure.
A range of products has been developed to repair delaminated surfaces, some with a polymer modified component which adheres strongly to the host concrete and can be applied as a thin layer. These are not popular with the conservation industry as they introduce different materials and will not weather-in to match the concrete.
Other techniques for repairing damage to concrete include epoxy injection to fill thin cracks, or concrete shotcrete for deeper cracks. These treatments can be very expensive but can have a good impact on the longevity of concrete structures.
Concrete repairs may be made by using a variety of materials and techniques, including dry packing, hydraulic cement, and concrete slurry or mortar. The choice of material will depend on the particular situation and the budget. For example, dry packing is often the most economical method but is not suitable for all situations.
A wide variety of bonding agents can be added to concrete repair mixes to improve adhesion. These chemicals, when painted onto the concrete surface before applying the repair, bind to the old concrete and help it to remain stable in a freeze-thaw environment.
Concrete repair can be hazardous work, particularly for large projects or repairs in high places. It is important to hire a professional concrete contractor who has the proper training and safety equipment to complete the project. A reputable concrete repair contractor should also offer warranties for their work and be insured.
Repairing Damaged Areas
Many concrete surfaces require a good deal of maintenance and repair to prolong their lives and reduce the need for costly replacement. A proactive approach to these repairs can help maintain a functional environment, while minimizing the impact on productivity and reducing downtime. The use of the right materials, proper construction practices and sound maintenance procedures will minimize the need for future repairs.
To identify the best solution for repairing damaged areas, it is important to understand that each situation is unique and requires a thorough inspection. A non-destructive evaluation (NDE) technique such as impact-echo or radar can reveal a lot about the condition of concrete without the need to break open it. A hammer and spray paint can also be used to identify delaminated or damaged areas by pinging the surface; sound concrete will give a hard ring while delaminated and weak concrete will ping with a dull hollow sound.
Once the extent of the damage is known, it is a good idea to use a handheld rotary power grinder to remove any unsound concrete and expose the underlying sound material. After the area is cleaned, it is important to outline the repair area with painter’s tape and etch the surface of the concrete to improve the bond with the repair materials.
While there are a wide variety of concrete repair products available, not all of them are created equal. It is important to consider the physical properties of each product and the requirements of the project, such as constructability, application methods and curing practices. A few of the most important properties include cracking resistance (drying shrinkage and modulus of elasticity), permeability, freeze-thaw durability and bond strength.
A good concrete repair product should have a low drying shrinkage and high modulus of elasticity. This is critical to a long term durable repair because the higher the drying shrinkage of a concrete repair, the greater the risk that it will debond from the parent concrete. Similarly, a high freezing and thawing durability will help ensure that the repair survives exposure to harsh conditions.