A well-executed mobile home remodel can breathe new life into a living space, increasing aesthetics and functionality. However, major renovations require balancing vision with budget.
Choosing a contractor who understands the unique construction aspects of mobile homes will help keep costs down. When evaluating contractors, ask about their licensing and insurance as well as for a list of references. Contact Mobile Home Remodeling Tacoma WA now!
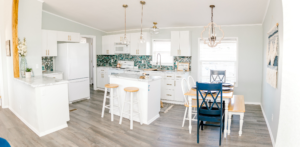
The interior of a mobile home can be upgraded to improve comfort, style, and functionality. Remodeling projects can be as simple as painting the walls or as complex as replacing countertops and cabinets. Before starting any project, it is important to develop a budget and identify the areas you would like to improve. It is also helpful to consider your long-term plans and whether or not your investment will yield a return in the form of a higher sales price.
Some remodeling projects can be completed as DIY projects, while others may require a professional contractor. It is important to evaluate your budget and priorities when determining the scope of your mobile home renovation. Start with the most critical areas, such as the kitchen and bathroom, and then expand to other rooms if you have additional funds available.
It is also essential to consider structural considerations when choosing materials for mobile home renovations. It is important to use light-weight materials that will not put undue stress on the mobile home’s frame or trusses. Additionally, moisture-resistant and energy-efficient options are ideal for mobile homes to help reduce utility costs.
Replacing flooring is an excellent way to transform the appearance and feel of a mobile home. New flooring can enhance a room’s aesthetic, create a more open space, and increase durability. It is important to choose a material that is easy to maintain and matches the existing style of the mobile home.
Adding or upgrading storage options is another easy way to upgrade a mobile home. Adding shelves or wall-mounted storage can increase the amount of usable space in a room. Alternatively, removing non-load-bearing walls can create an open floor plan. Adding built-in storage can be an effective solution for creating more space in a mobile home without increasing the size of the structure.
Adding a backsplash to the kitchen can protect the walls from damage caused by water and food particles. Moreover, it can enhance the visual appeal of the room and provide an opportunity to incorporate a splash of color. It is also a good idea to install energy-efficient lighting in the kitchen to reduce utility bills and add to the overall efficiency of the mobile home.
Exterior
When it comes to mobile home remodeling, determining your budget is an essential first step. This will help you determine the scope of your project and set realistic expectations for costs. If you are on a tighter budget, there are still several great ways to make a significant impact on the outside of your home.
New window and door replacements will not only increase the curb appeal of your home but also boost its energy efficiency. You can choose from a variety of styles and materials to fit your aesthetic and your budget. If you are looking for a more dramatic impact, try adding bay windows or installing awnings to shade and add privacy to your outdoor space.
Adding a front porch or deck is another way to upgrade your mobile home’s exterior while enhancing its function and curb appeal. This is a relatively inexpensive improvement, but it can make a huge difference in your home’s overall appearance. It’s also a good idea to consider the addition of a small BBQ or outdoor dining area.
Skirting is one of the most cost-effective but valuable mobile home remodel projects you can undertake. It serves the important purpose of regulating the temperature under your mobile home, but it can also increase its curb appeal by adding color and texture. You can choose from a variety of skirting options, including vinyl, cinder block, and rock.
While you’re at it, consider upgrading your door frames and hardware. You can easily replace your original doors with sliding doors to improve the look of your mobile home and give it a more modern feel. Alternatively, you can install new doors with decorative features such as barn doors or wrought iron doors to complement your style.
Another simple but effective mobile home remodel is scrapping and retexturing your ceilings. Mobile homes used to use a popcorn texture that gives them a “trailer” feel, so it’s a good idea to get rid of this outdated material and opt for a smooth ceiling.
For a more dramatic effect, you can also invest in a new roof and siding. While this is a more expensive option, it can drastically improve your mobile home’s curb appeal and help you save on your energy bills in the long run.
Storage
If your mobile home needs a boost in storage space, consider the many options available. Creative solutions can maximize your space and help keep you organized. Look for overlooked spaces, such as the water heater closet, which can serve as a convenient place to store items that clutter your home. Shelving systems are another simple yet effective way to improve your home’s storage. They come in a variety of shapes and sizes, from single shelves to complete closet shelving systems with spots for bottles, cans, boxes, and more.
You can add storage space by remodeling your kitchen and bathroom. Updated fixtures and cabinets can breathe new life into these vital rooms, while creating a cohesive design that fits your style and functional needs. Adding hardwood floors is another easy and cost-effective way to add value to your mobile home. These versatile materials are long-lasting and can complement any design theme.
The entryway of your mobile home sets the tone for the entire interior, so it’s important to create a welcoming entrance that’s both inviting and well-lit. A fresh coat of paint, updated door hardware, and a simple welcome mat can make a big difference. You can also add a bench or other seating to provide an inviting spot to enjoy the outdoors.
Adding natural light is a great way to brighten up your mobile home and can make it feel more cozy and fresh. Consider replacing small windows with larger, energy-efficient ones that let in more light and cut down on electricity costs. Investing in skylights is another great option and can significantly improve the lighting in a room.
Whether you choose to tackle your mobile home remodel DIY or hire professionals, it’s essential to carefully plan the project and set a budget. A reputable professional will be able to provide valuable insights and guidance throughout the process, while keeping your vision and budget in mind. For more complex projects, such as electrical or plumbing work, it is always best to enlist the help of qualified professionals. If you are tackling the project yourself, be sure to use safety precautions and wear proper attire and protective equipment when handling potentially dangerous tasks. For large or time-consuming remodels, PODS offers portable storage containers in a range of sizes to meet any size remodel and can be kept on your property until the job is done.
Energy Efficiency
Mobile homes are prone to structural wear and tear over the years. This means that renovations are a necessity to keep the home in good shape and up-to-date. Remodeling can help fix issues like flooring, roofing, plumbing and foundations. It also allows for upgrades that can enhance the aesthetic and improve the energy efficiency of a mobile home.
One of the best ways to make a mobile home more energy efficient is by installing new doors and windows. This will help regulate the temperature and reduce the strain on the HVAC system. In addition, new doors and windows will provide a more stylish look. There are a variety of options available for door and window replacement that can fit any budget.
Another great way to boost your mobile home’s energy efficiency is by adding insulation. This will help keep the home warmer in the winter and cooler in the summer. You can use spray foam or blown-in insulation for maximum benefits. You should consult with a professional to determine which type of insulation is right for your mobile home.
Lighting is another area where you can save on energy costs by replacing existing lights with new, more efficient fixtures. You should choose fixtures that complement the design theme of your mobile home, and opt for light fixtures that are made with LED technology. This will help you save money on your electricity bills and can increase the resale value of your home. Be sure to consult local codes and regulations before undertaking any electrical work in your mobile home.
The crawl space under your mobile home is a perfect place to add insulation. It will prevent excess heat from escaping, and it can be done without having to remove any walls. You can also add skirting to prevent the crawl space from absorbing moisture. It is important to ensure that any ductwork under your mobile home is properly vented. Failure to do so could result in carbon monoxide buildup in the crawl space, which is dangerous for your family.
Whether you are looking to make small cosmetic changes or major renovations, it’s important to consider your budget and timeline when planning a remodel. It is also critical to prioritize structural repairs over cosmetic updates.