3D Printing is a manufacturing technique that uses an additive process to build models layer by layer. The model is created from a digital file that contains “coordinates” for where the material should be placed.
Companies are using 3D Printing for rapid manufacturing in addition to prototyping. Automobile manufacturers, for example, use it to print spare parts, jigs, and end-use parts. Click https://www.by3design.com/ to learn more.
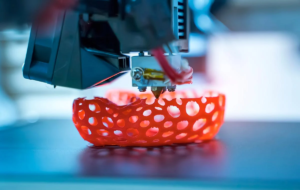
Rapid prototyping (RP) is an important tool for product development that helps designers make prototypes and improve their designs based on user feedback. It also enables engineers to make changes to their design before moving forward with the production of a new product. This allows for a faster turnaround time and reduces the risk of making costly mistakes in the final production process.
Using 3D printing technology, a prototype can be made in a matter of days or weeks. This saves time and money in the manufacturing process and makes it easier for companies to test their products with real users. It can also help reduce the need for traditional manufacturing processes such as CNC machining and injection molding, which can be expensive and time-consuming.
3D Printing is a form of additive manufacturing (AM) that uses laser-induced melt processes to create complex shapes and structures. It can be used for a wide range of applications, including engineering product design, rapid manufacturing, and medical devices. The 3D printing industry is developing rapidly and has become a key player in the manufacturing sector. The industry is expected to grow to over $80 billion in 2025.
A prototype is a model that represents a physical part or assembly using three-dimensional computer-aided design data. It is used in the design and evaluation of a product, and it can be made from plastics, metals, or ceramics. It can be a mock-up of a design, or it can look like the finished product. Prototypes can be low-fidelity or high-fidelity, and they can vary in appearance, size, and function.
The best way to get the most accurate and reliable feedback on your product is to test it with users. This will ensure that your product is designed for people and is working as intended. It will also help you find problems and fix them before the product launches. However, it is important to understand that a prototype is just a representation of a finished product, and it may not work exactly as the final version.
When testing your prototypes, it is important to avoid distractions and information overload. To maximize your results, you should try to focus on a specific element of the flow or feature that you want to test. You should also limit the number of participants to keep the test time and cost down. For example, if you are testing a mobile app, you should only test it with users who meet your target personas.
Customization
Customization using 3D printing technology allows companies to offer products tailored to the needs and preferences of consumers. This type of customization can help companies build brand loyalty and increase customer satisfaction. It is also a great way to reduce manufacturing costs. Unlike traditional manufacturing, which requires costly tooling changes for new specifications, 3D Printing allows manufacturers to quickly and cost-effectively produce personalized products.
To make a product printable, 3D printers use digital models of the product, which are mathematical representations of the three-dimensional surface created with computer-aided design (CAD) software or developed from 3D scan data. These models are then sliced into horizontal cross-sections for Printing. The sliced model is then sent to the 3D printer, which builds it layer by layer until the desired object is completed.
Consumer-facing companies are using 3D Printing to personalize their products, including clothing, furniture, and electronics. The ability to print on demand also helps businesses save on inventory and distribution costs.
In addition, 3D Printing can be used to create specialized tools that streamline manufacturing processes. For example, industrial equipment company Protolabs Network uses 3D Printing to produce jigs and fixtures that allow workers to efficiently service and operate their machines. 3D Printing is also transforming the automotive industry. BMW has partnered with Shapeways to enable customers to customize their vehicles’ interiors with personalized accessories and components. These accessories include cup holders, dashboard trims, and even personalized insoles for increased comfort.
With the right customization technology, consumers can be engaged in the design process, which leads to a greater feeling of attachment to the final product. In turn, this creates a deeper emotional connection with the brand and fosters loyalty. In addition, mass customization enables businesses to gather valuable consumer data and improve marketing efforts. Moreover, the speed of production with 3D Printing also helps to shorten the design cycle and reduce time-to-market. This is particularly important for new products, where numerous design iterations are necessary before they can be launched on the market.
Reliability
3D Printing is a versatile and reliable manufacturing technique that can produce durable parts. It can be used to create a wide range of materials, including plastic, metal, and ceramics. In addition, the process is fast, affordable, and accurate. It can also be used to prototype products and manufacture components on demand. However, the technology can be vulnerable to error, such as incorrect print settings or filament jams. To reduce the risk of error, it is recommended to use DFM techniques and work with an experienced manufacturer.
The development of 3D Printing has allowed for the creation of highly complex structures that would be impossible to replicate with traditional methods. These structures are useful in fields such as aerospace, medical, and automotive engineering, where they can be utilized to test and improve existing designs. In addition, they can be used to create spare parts for older vehicles, reducing the cost of maintenance and repairs.
Using 3D printers to fabricate complex objects requires a unique blend of technical, creative, and analytical skills. This technology has transformed the way we work and think, allowing us to create new products and solutions at a rapid pace. It has also revolutionized education, making it possible for students to explore complex concepts by turning them into tangible models. Whether it’s a historical artifact, intricate geometries in math, or a cross-section of the human body, 3D Printing allows students to gain a deeper understanding of difficult subjects.
As a result, many industries are leveraging 3D Printing to increase productivity and improve performance. The automotive industry, for example, is using the technology to develop lighter and stronger car parts that can reduce fuel consumption and improve engine performance. It is also enabling them to test and launch new designs more quickly, cutting costs and time to market. Additionally, custom and specialized parts can be manufactured for vintage cars to maintain their originality and value.
3D Printing has also become a popular tool in medicine and healthcare, where it can be used to produce surgical tools and replacement body parts. It can also be used to create prosthetics and other devices that enhance mobility for people with physical disabilities. It can help patients recover faster and feel more comfortable in their daily lives. In addition, 3D Printing can be used to print organs for transplantation, which can significantly reduce the number of patients who need to wait for a donor.
Efficiency
With 3D Printing, companies can rapidly move from a computer-aided design (CAD) drawing to a physical prototype. This allows for quicker iterations, which can improve products and decrease the time to market. Additionally, the layer-by-layer printing process reduces waste. Furthermore, the technology can produce complex shapes and parts that would be difficult or impossible to create using traditional manufacturing methods.
Another advantage of 3D Printing is its ability to create strong and lightweight parts. This is particularly important for industries such as automotive and aerospace, where weight savings can translate into significant fuel savings. For example, 3D printed titanium components are up to five times lighter than their solid metal counterparts and can be produced in a fraction of the space. This technology also enables engineers to explore new design practices, such as topology optimisation, which can optimise a product’s shape without compromising its strength.
The range of materials used in 3D Printing is vast and includes flexible polymers, sturdy metals, and ceramics. In addition, there are specialized materials like conductive filaments and glow-in-the-dark plastics that expand the capabilities of 3D printers. These materials are useful for a variety of applications, from prototyping to creating custom medical devices.
Unlike conventional manufacturing processes, 3D Printing uses only the material needed for a particular part, which reduces resource consumption. This can save companies money on materials, as well as reduce production and inventory costs. Moreover, the ability to produce parts on-demand eliminates the need for costly tooling, which can be a major expense when producing low volumes of a product.
While some experts argue that 3D Printing is not a sustainable technology, it is still more environmentally friendly than many other production methods. It is less energy-intensive than injection molding and CNC milling, and can be used to produce spare parts for existing machines. In addition, it can be used to produce a wide range of materials, including biodegradable polymers and living cells. This opens the door to innovative new designs and potential applications, such as regenerative medicine and personalized healthcare. Additionally, the ability to print in-house gives manufacturers tighter control over their intellectual property, reducing the risk of data leaks or theft.